Have global and domestic factors affected designers’ supply chains?
International supply chains have been disrupted by global and domestic factors in the last few years, but how has this affected designers and where do they source materials from now?
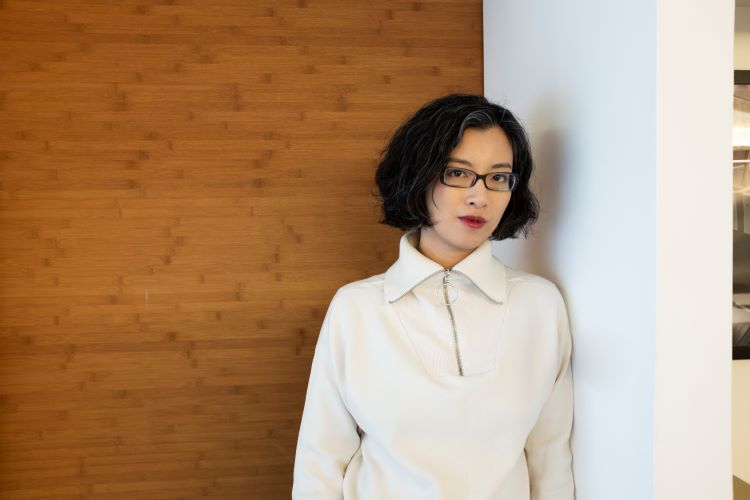
European textiles and surface finishing products tend to be the highest quality and are the most desirable. Previously we used to source a lot more European suppliers for projects in the far East, but now it takes longer lead times to deliver. Now we tend to give clients two choices: a high-quality European supplier and a closely matched local alternative. However, if clients want something urgently, they tend to have less options now.
Tangerine director Weiwei He

Glass, wood and microchips are just three from a long list of items affected by supply chain issues. Unfortunately, the nature of our work means we can’t do without them, so instead we’re having to be thoughtful and flexible about how we specify them. Our projects can be anywhere from six months to six years in length. For longer projects, we are flagging long-lead items like showcases right at the beginning and working with our clients to find creative ways of navigating procurement regulations. On all projects, but especially the shorter-run ones, we are looking at how we can adapt standard products – this is particularly true of digital installations.
We are doing a lot of digging into where products are coming from. We are sourcing as much material as possible close to home – either where the client is or where the contractors are. We are also acutely aware of ethical issues. For example, a lot of plywood has typically been sourced from Russia, but this is not an option for us now.
With all of this said, flexibility and creative adaptation are fundamental to sustainable design so I think many of our current approaches to sourcing materials are here to stay.
Event Creative Director Eithne Owens
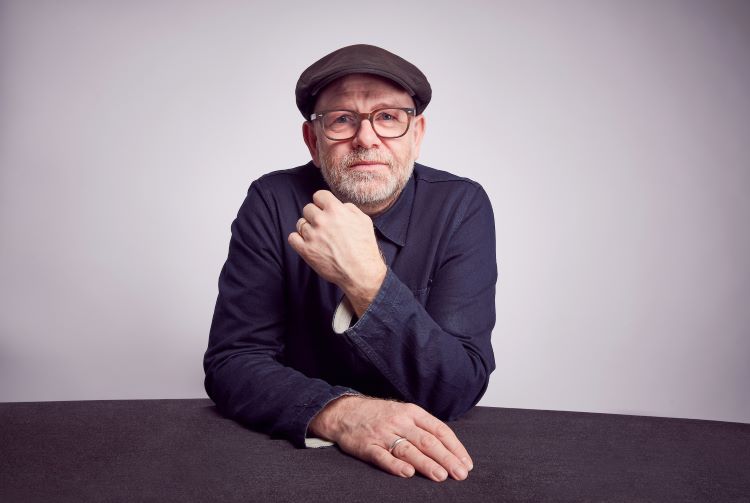
Against the disruptions of recent years, the principles of globalisation and just-in-time systems of production have proven to be fragile and lacking in resilience. In the UK, friction-free trade has been upended by Brexit. Exporting has become problematic and our markets have shrunk as a result.
During Covid, first demand and then production almost completely ceased. Once demand returned, there was a huge lag time in recovery. The difference between supply and demand has increased material, production, transport and, in turn, finished-production prices. There has been a concomitant increase in freight costs – to as much as $20,000, (£17,600) per container from the Far East to the UK or US. As a result of all this, demand for UK-made goods has understandably increased.
As an industry, we are having to rethink materials. For example, a breakdown in lumber supply chains has created a huge shortage of one of the most popular woods, European oak. In its place, manufacturers are turning to less widely used woods such as red oak and even cherry from North America.
The conflict in Ukraine has increased global energy prices, which quickly trickles down to impact transport, material and – again – production costs. On top of all that, the extreme devaluation of the pound as a result of new government policy is adding to the import costs of parts and raw materials.
To survive these multiple layers of turmoil, manufacturers are having to pass on the shock costs at remarkable speed, adding Covid surcharges, Brexit surcharges, energy surcharges, and so on. It is a highly challenging environment.
Pearson Lloyd co-founder Tom Lloyd
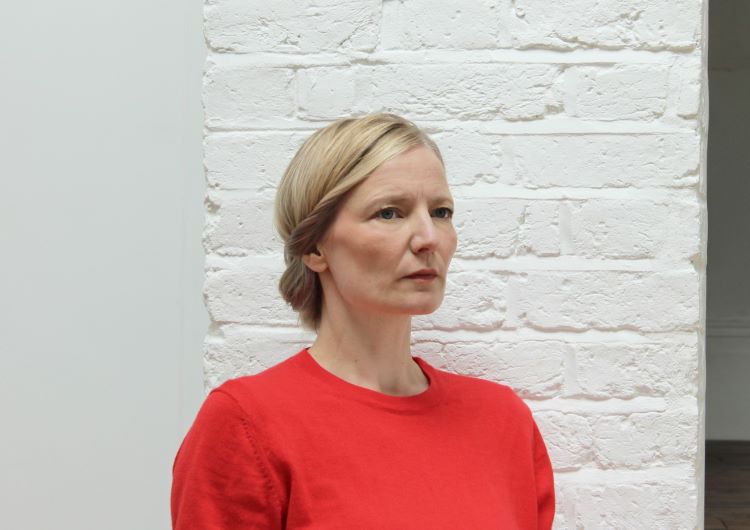
In the last few years we are increasingly experiencig difficulties receiving competitive tenders for a variety of projects. The problems seem to be two-fold; expensive materials due to supply chain issues as well as a lack of skilled affordable labour. For existing projects this often means more complex tender processes like the splitting up work packages to attain a number of valid tender submissions. For new or current projects the design process has to take on board the difficult climate and design developments needed to work towards solutions that avoid known shortages and ideally keep supply chains local.
Studio founder and designer Gitta Gschwendter

At Morrama, we onboard our manufacturing partners during the design phase to help us understand the parameters for design and costs for production methods. We maintain the relationship with our factory counterparts using WeChat in-app translations if they are based in Asia. However, for the past two years, we have seen a massive disruption in the supply chains.
We had to adjust our design processes and focused on maximum transparency with clients and manufacturers to maintain the relationships. We have also invested in localised production methods, especially where we can create on-demand. Working with our office neighbour, 3D company batch.works, we design products that could be ordered and made as needed. This idea is not new, but as technology advances, the ability to utilize waste streams as the raw material for new products is becoming a reality. Furthermore, we hope that a send back scheme would allow old products to be returned and remade into a fresh new design.
Where possible, we would champion that our clients bring their production into the UK or Europe as it offers better shipping, security and reduced emissions.
Morrama Associate Director Andy Trewin Hutt
Dear Sirs,
Please be more attentive to words used. It is not ‘The conflict in Ukraine’ as you wrote but ‘Russian invasion to Ukraine’. Accurate wording is also part of design communication. Please respect those who suffer. Kind Regards, Slawek Kluziak, CEO/Global Branding Director at SiebertHead.com